Rezultate obtinute in cadrul fazei 1, decembrie 2017
Optimizarea procesului de sintetizare a grafenei prin metoda CVD
Optimizarea procesului constă în modificarea, pe rând, a parametrilor de proces: temperatură, presiune, debit de gaz, timp de depunere, pentru a obţine grafenă monostrat, cu domenii cristaline mari, pe o arie cât mai largă şi de calitate comparabilă cu cea comercială. Dacă în timpul experimentelor preliminarii de implementare s-a obținut grafenă pe aproximativ 40% din suprafața foliei de cupru, în cadrul proceselor experimentale de optimizare se urmărește un grad de acoperire de cel puțin 90%.
Pe probele optimizate s-a ajuns la un grad de acoperire de peste 90%, cu domenii de grafenă cu diametrul între 50 µm și 150 µm, iar spectrele Raman achiziționate confirmă obținerea unui monostrat de grafenă, cu defecte minime și o calitate foarte bună. Benzile Raman G și 2D sunt specifice grafenei monoatomice, în timp ce lipsa benzii D în locațiile investigate este un indicator al calității. Valoarea raportului I2D/IG se află în intervalul 3.16 - 3.6, valoarea mult mai mare decât 2 arătând existența fără echivoc a grafenei monostrat. Lărgimea la semiînălțime a benzii G se află în intervalul 10.92- 16.38 cm-1 fiind apropiată de valoarea de echilibru 15 cm-1. Lărgimea la semiînălțime a benzii 2D se află în intervalul 30.57 - 21.62 și certifică prezența grafenei monoatomice în zonele investigate.
|
|
Imagine SEM: domenii de grafenă crescute pe substrat de cupru. Imaginea surprinde un proces de creștere incomplet, cu domenii care variază între 50 µm și 150 µm
|
Imagine SEM: grafenă crescută uniform pe substrat de cupru. Imaginea surprinde un proces de creștere complet, domeniile de grafenă formează un film continuu pe suprafață și acoperă în totalitate suprafața catalizatorului.
|
|
Spectru Raman: grafenă pe sybstrat de cupru. Picurile G și 2D, 1581 cm-1 și 2631 cm-1, precum și raportul I2D/IG > 2, confirmă prezența grafenei monostrat. |
Fabricarea membranelor de grafenă
Tehnicile de transfer ale grafenei trebuie să rezolve două probleme principale: 1) separarea stratului de grafenă de pe substratul de metal catalizator şi 2) protecţia integrităţii grafenei după separare. Metodele de obţinere a a filmelor de grafenă CVD pe un substrat de interes pot fi clasificate în trei mari categorii: (1) tranferul cu ajutorul unui strat cu rol de suport pe substratul de interes, (2) transferul fără strat cu rol de suport pe substratul de interes şi (3) creşterea directă a grafenei CVD pe substratul de interes fără alt pas de tranfer.
Rutele de transfer ce utilizează un polimer cu rol de suport, sunt cele mai exploatate metode, în care un film subțire de polimer este depus, ca un nou suport, pentru grafena crescută, pentru a îndepărta suportul metalic prin corodare sau delaminare electrochimică. Polimetilmetacrilatul (PMMA), polidimetilsiloxanul (PDMS) și straturile de policarbonat sunt raportate ca fiind cele mai bune suporturi pentru transferul grafenei pe diferite substraturi de interes, cu înlăturarea secvențială a polimerului cu ajutorul unor solvenți organici.
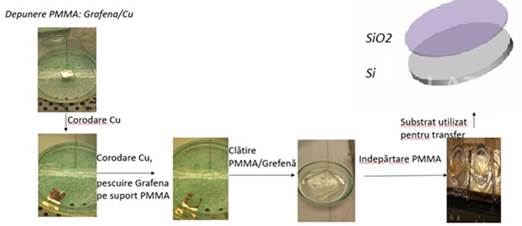 |
Schema de transfer a grafenei monostrat de pe folie de cupru pe siliciu oxidat |
Experimentele preliminare de transfer au fost efectuate pe substrat de Si tip p și n, orientare cristalografica <100>, tăiat în bucăți de 20 mm x 20 mm, cât și pe Si oxidat termic, grosimea SiO2 fiind de 300 nm.
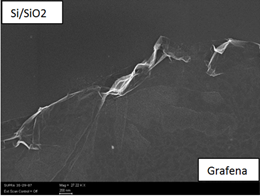 |
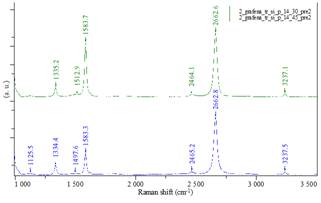 |
Morfologia suprafeței de Si/SiO2 și evidența domeniilor de grafenă transferate |
Spectre Raman pentru grafena pe substrat de Si/SiO2, după etapa de transfer. Cu verde o zonă în care grafena s-a exfoliat și s-a pliat formând un strat dublu. Cu albastru o zona de grafenă monostrat |
Fabricarea orificiilor și obținerea membranelor
Pentru fabricarea membranelor, am transferat grafenă crescută pe folie de cupru peste orificii fabricate într-o plachetă de siliciu, orientare cristalografică <100>, de tip p, cu grosimea de 175 µm +/- 25 µm, polisate dublu-față. În figura este prezentat layout-ul măștii cu orificii de 9 µm, iar în medalion este prezentat un detaliu.
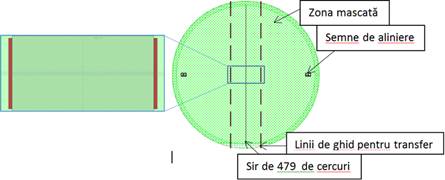 |
Layout mască fotolitografică pentru fabricarea orificiilor cu diametrul de 9 µm. În medalion este prezentat un detaliu al zonei centrale, pe centru se observa un șir de cercuri (pe verticală, la jumătatea distanței dintre cele două linii de ghid) |
Pentru a menține diametrul orificiilor cât mai aproape de cel proiectat, gravarea oxidului de siliciu se face în doi pași: un pas de corodare uscată în plasmă, urmat de un proces scurt de corodare umedă. Corodarea uscată s-a făcut în sistemul de corodare cu ioni reactivi (RIE – Reactive Ion Etching) folosind un amestec de Ar : CHF3, în raport 4:1, la presiunea de 10 Pa, și putere de radio-frecvență de 250 W. Viteza de corodare a fost de aproximativ 45 nm/min, procesul fiind oprit după 6 minute, pentru a coroda în total aproximativ 270 nm de oxid (din totalul de 300 nm grosime crescută termic).
Nu am permis corodarea completă a stratului de oxid prin această metodă, deoarece în cazul acestui proces există tendința de corodare neuniformă a substratului de Si, care crește semnificativ rugozitatea. Ultimii 30 nm de oxid rămași au fost corodați în soluție BHF (NH3 : HF, 6:1), timp de 30 s. Corodarea substratului de siliciu pentru a obține orificiile s-a făcut în echipamentul de corodare cu plasmă cuplată inductiv (ICP – RIE), folosind un proces clasic de alternare a gazelor (proces Bosch). După corodarea siliciului, reziduurile de fotorezist de pe fața plachetei au fost îndepărtate în plasmă de oxigen, timp de 10 minute. În figurile 2.5 și 2.6 sunt prezentate imagini cu rezultatele obținute în urma fabricării orificiilor cu diametrul de 9 µm. Măsurătorile făcute pe imaginile optice arată diametrul de intrare de ~8,5 µm în timp ce diametrul de ieșire este de ~7,5 µm.
Pentru obținerea membranelor de grafenă, s-a transferat grafenă de pe folia de cupru pe substrat de Si/SiO2 structurat cu orificiile cu diametrul de 9 µm. În figura 2.7 sunt prezentate imagini SEM cu un strat monoatomic de grafenă transferat peste un orificiu de 9 µm.
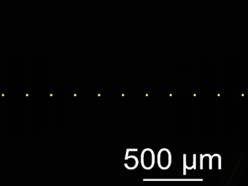 |
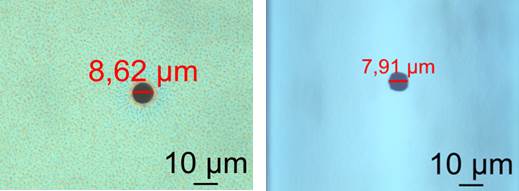 |
/Figura 2.5: Imagine optică, mărire 20x, iluminare de jos. Serie de orificii de 9 µm cu spațiere de 200 µm |
Figura 2.6: Imagine optică, mărire 100x. (dreapta) Orificiul corodat văzut de pe fața plachetei. De jur imprejur se poate observa stratul de oxid, afectat de procesul de corodare al siliciului. (stânga) Orificiul corodat văzut de pe spatele plachetei. |
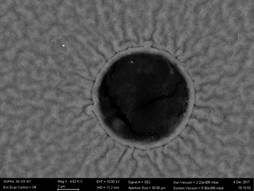 |
 |
Orificiu peste care a fost transferat grafenă monostrat |
Membrană de grafenă peste un orificiu fabricat, de jur împrejur se observă filmul polimeric de PMMA folosit la transfer |
Evaluarea activității antibacteriene
Pentru realizarea experimentului filmele de grafenă au fost aplicate direct pe substraturi de cupru și siliciu, prin tehnica CVD (depunere chimică din fază de vapori). Fiecare grafenă din monostrat avea o grosime de 35 microni și o suprafață de 2 cm2 . În experiment au fost testate şase tipuri de substraturi: cupru cu grafenă; cupru fără grafenă; siliciu tip p cu grafenă; siliciu tip p fără grafenă; siliciu tip n cu grafenă; siliciu tip n fără grafenă.
Analiza rezultatelor obţinute în urma testărilor indică supremaţia activităţii antibacteriene evidenţiată în cazul substraturilor de cupru cu grafenă.
În cazul testărilor efectuate cu bacteria Staphylococcus aureus există diferenţe semnificative ale activităţii antibacteriene la cele 6 substraturi analizate. Valorile obţinute exprimate în unităţi formatoare de colonii (UFC) indică existenţa unei activităţii antibacteriene superioare la toate cele 3 suporturi pe care a fost depusă grafena.
Testele efectuate cu bacteria Escherichia coli indică o activitate bacteriană mai redusă comparativ cu cea semnalată la stafilococi. Este posibil ca peretele bacterian altfel structural la bacteriile Gram negativ să confere acestor bacterii o rezistenţă mai mare la acţiunea monostratului de grafenă. Valorile obţinute indică clar o reactivitate mai scăzută.
Monostratul de grafenă are acțiune antibacteriană inhibând viabilitatea bacteriilor venite în contact cu el. Cunoscând o serie de proprietăți fizice specifice grafenei se poate afirma că ea se comporta ca o pompă de electroni. Fenomenele generate de grafenă interferă cu mecanismele intime de transport electronic de la nivelul membranei citoplasmatice bacteriene generând un stress oxidativ. Grafena este un excelent acceptor de electroni ceea ce duce la tranferul electronilor din membrana citoplsmatică bacteriana la nivelul cuprului. În acest mod lanțul respirator bacterian este grav afectat având consecință pierderea viabilității.
Pentru detalii: [email protected].
Fabricarea senzorului de presiune pe bază de grafenă
Membranele de grafenă monoatomice au proprietăți mecanice remarcabile, fiind capabile să reziste la presiuni de până la 8 GPa. Datorită modului de transport electronic specific monostraturilor de grafenă, deformări mici ale suprafeței pot să inducă modificări semnificative în conductivitatea electrică a materialului. Pe baza acestui fenomen dorim să explorăm posibilitatea fabricării unor senzori electro-mecanici pentru măsurarea presiunii în microdispozitive fluidice.
Pentru acest scop, s-a proiectat un sistem de microcanale fluidice, care să fie fabricat pe spatele unei plachete în care au fost corodate orificiile de 9 µm, descrise anterior. Pentru obținerea sistemului de microcanale fluidice pe spatele plachetei, s-a folosit procesul Bosch pe echipamentul de corodare cu plasmă cuplată inductiv. Ca strat de mascare s-a folosit fotorezist AZ 4562 cu grosimea de 6,2 µm, și oxidul de siliciu cu grosimea de 300 nm crescut în faza inițială de pregătire a plachetelor. Oxidul de siliciu a fost corodat în doi pași, conform procedurii detaliate în capitolul 2. Adâncimea corodată a fost de aproximativ 150 µm.
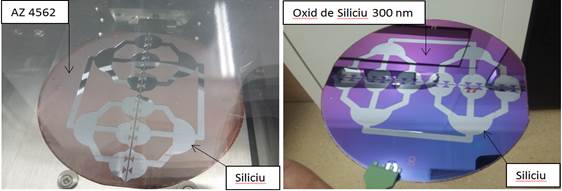 |
Sistemul de microcanale fabricat pe spatele plachetei de siliciu: (stânga) înainte de îndepărtarea fotorezistului AZ 4562; (dreapta) după îndepărtarea fotorezistului
|
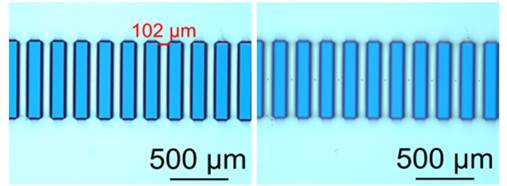 |
Zona centrală a sistemului de microcanale, imagine optică, mărire 20x, oxidul de siliciu este albastru intens: (stânga) focalizare pe partea superioară a pereților de separare, (dreapta) focalizare pe fundul microcanalelor, se observă orificiile deschise prin corodare de pe fața plachetei |
Fabricarea sistemului de microcanale integrat în placheta de siliciu a introdus o problemă care nu a fost anticipată. Practic, după fabricarea acestuia, procesele suplimentare de fabricare necesare caracterizării senzorului de presiune trebuie continuate pe o membrană de siliciu cu grosimea de aproximativ 50 µm. Transferul grafenei s-a putut face cu succes folosind procedura descrisă anterior, dar manipularea plachetelor, și procesarea ulterioară a devenit extrem de dificilă. Inclusiv pasul de fierbere în acetonă pentru îndepărtarea filmului de PMMA folosit la transfer, în unele cazuri a fost suficient de agresiv pentru a introduce stres suficient ca să rupă membrana de siliciu. În continuare pașii de metalizare a suprafeței și corodare a metalului pentru a fabrica padurile de contactare electrică au fost imposibil de realizat. Astfel, constatând că senzorul inițial proiectat nu este fezabil pentru fabricare am decis reproiectarea acestuia folosind ca element de bază emisia în câmp a unei matrici de structuri piramidale configurată în siliciu de tip n, cu conductivitate electrică mare.
[mergi la pagina principala] |